Custom Metal Spinning Manufacturer in China
Get a factory price — Start from Low MOQ
As an expert manufacturer, CJ provides high-quality Custom CNC Metal Spinning solutions to enhance your production efficiency and precision.
Higher Precision, Greater Efficiency
Enhancing productivity with advanced CNC metal spinning technology for precision forming.
Lower MOQ, More Flexibility
Custom solutions with small batch production, ensuring cost efficiency and adaptability.
Certified Products, Safety Guaranteed.
ISO-certified manufacturing with strict quality control, ensuring reliable and durable metal spun parts.
Spinning Parts Gallery
About CJ
With 30 years of expertise, CJ leads in CNC metal spinning technology, manufacturing, and sales. Our commitment to innovation led us to establish a metal spun parts division, utilizing our advanced machinery for premium accessory production. As China’s premier metal spinning industry expert, CJ integrates cutting-edge CNC software and Siemens control systems, delivering precise, efficient, and high-quality metal forming solutions
Factory Image
A few Spun parts we have done
Explore some of our high-quality spun and flanged components, engineered for precision and durability. Each part is manufactured using advanced metal spinning and flanging techniques to meet industry standards. Our expertise covers a wide range of applications, ensuring optimal performance for various industries.
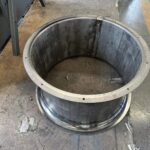
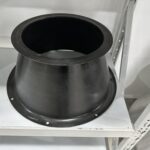
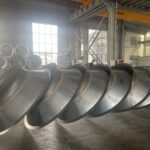
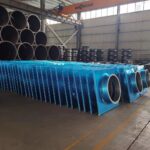
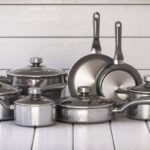
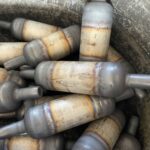
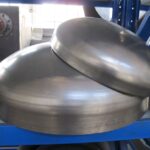
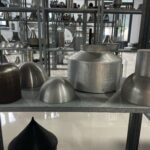
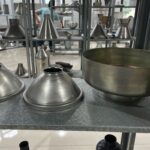
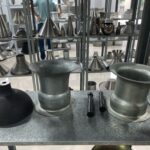
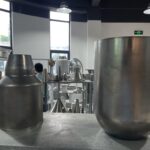
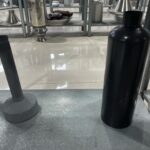
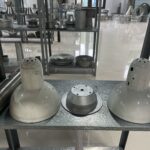
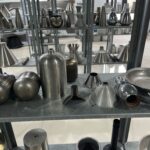
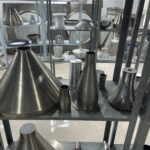
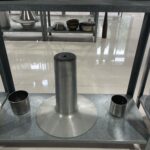
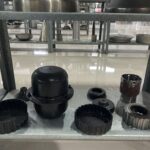
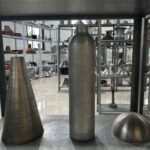
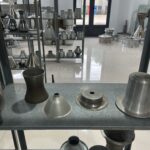
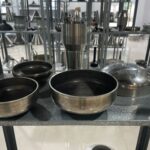
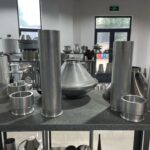
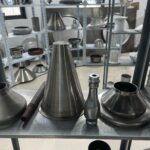
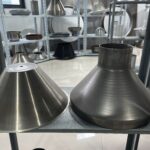
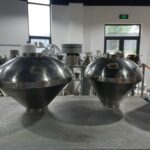
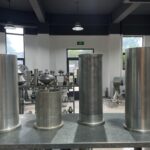
Why Choose CJ
CJ Industry, with over 30 years in CNC metal spinning, leads China’s market with precision CNC lathe technology. We deliver cost-efficient, superior-quality metal spun parts, excelling in rapid production and tight tolerances. We provide comprehensive solutions tailored to a diverse range of metal forming fabrication.
30 Years’ manufacturing Experience
20+ Years' Export Experience
24/7 Online Customer Support
Fast Delivery
Warranty Coverage
automatic solution design
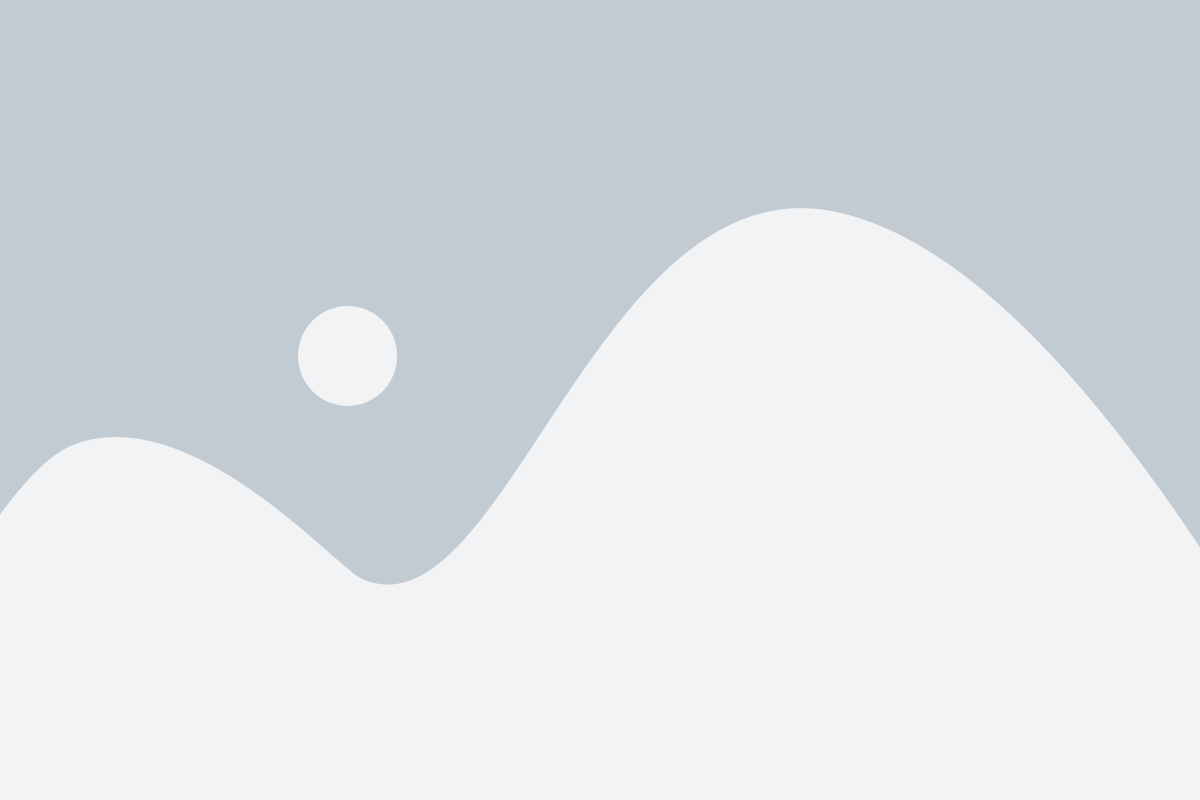
Our customers say
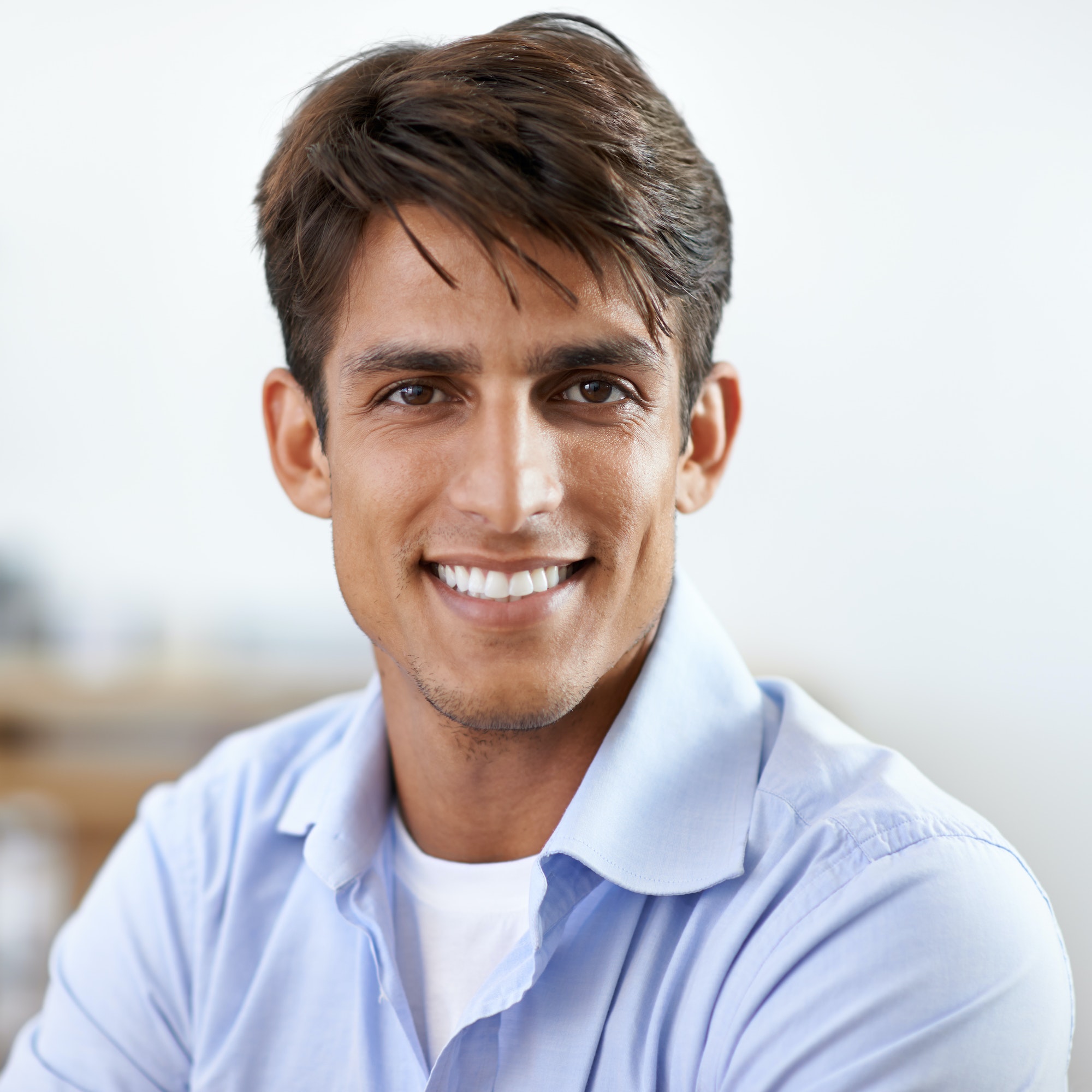
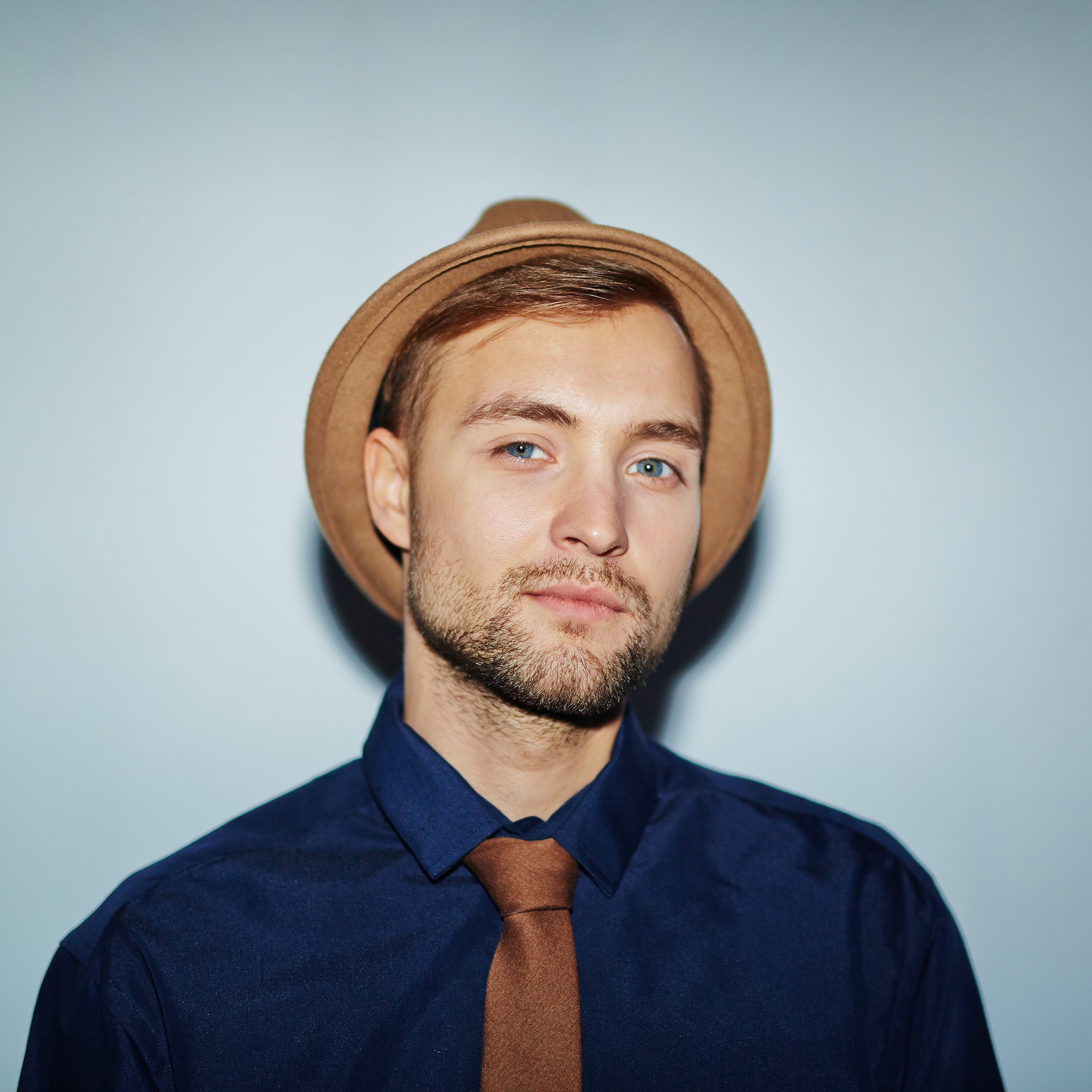
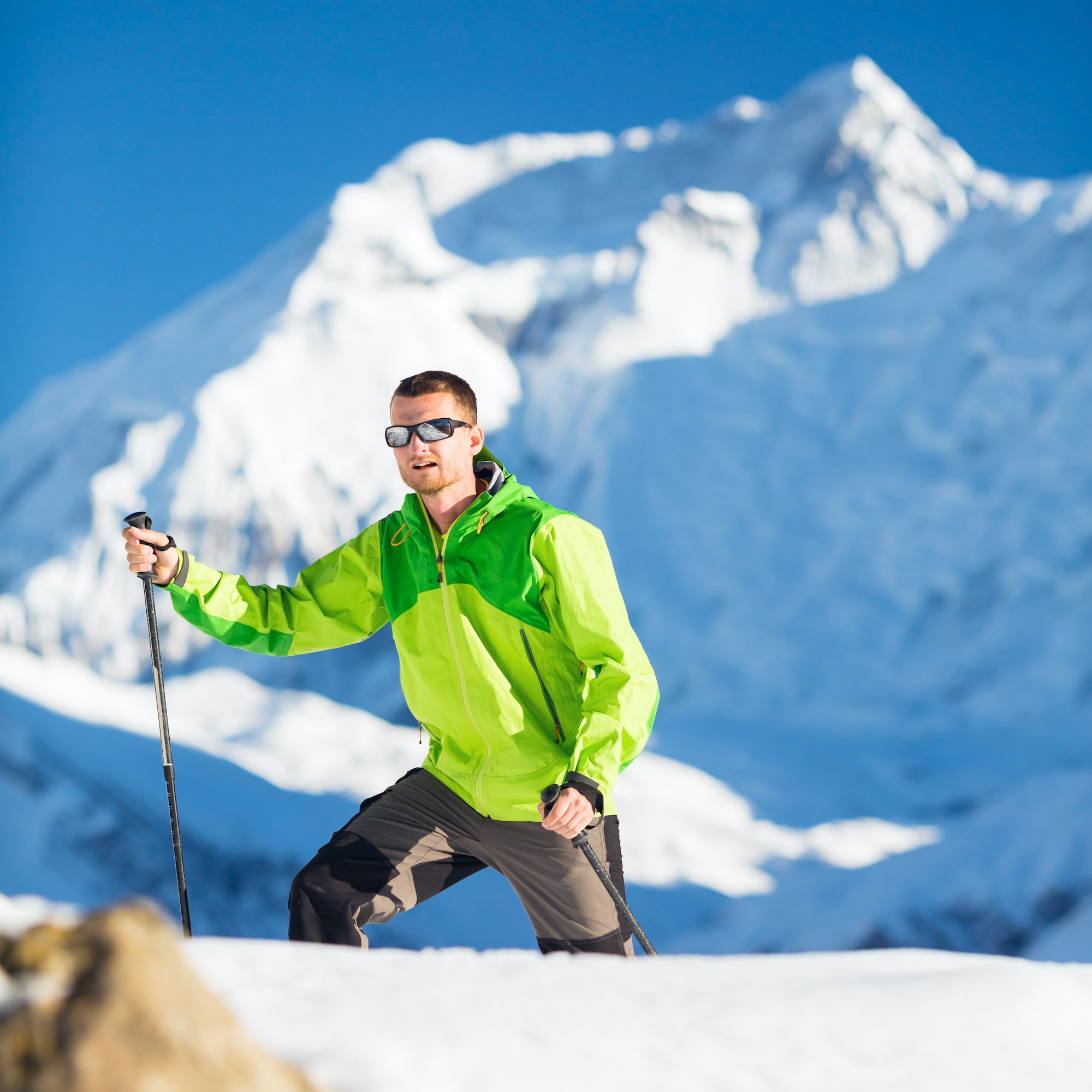
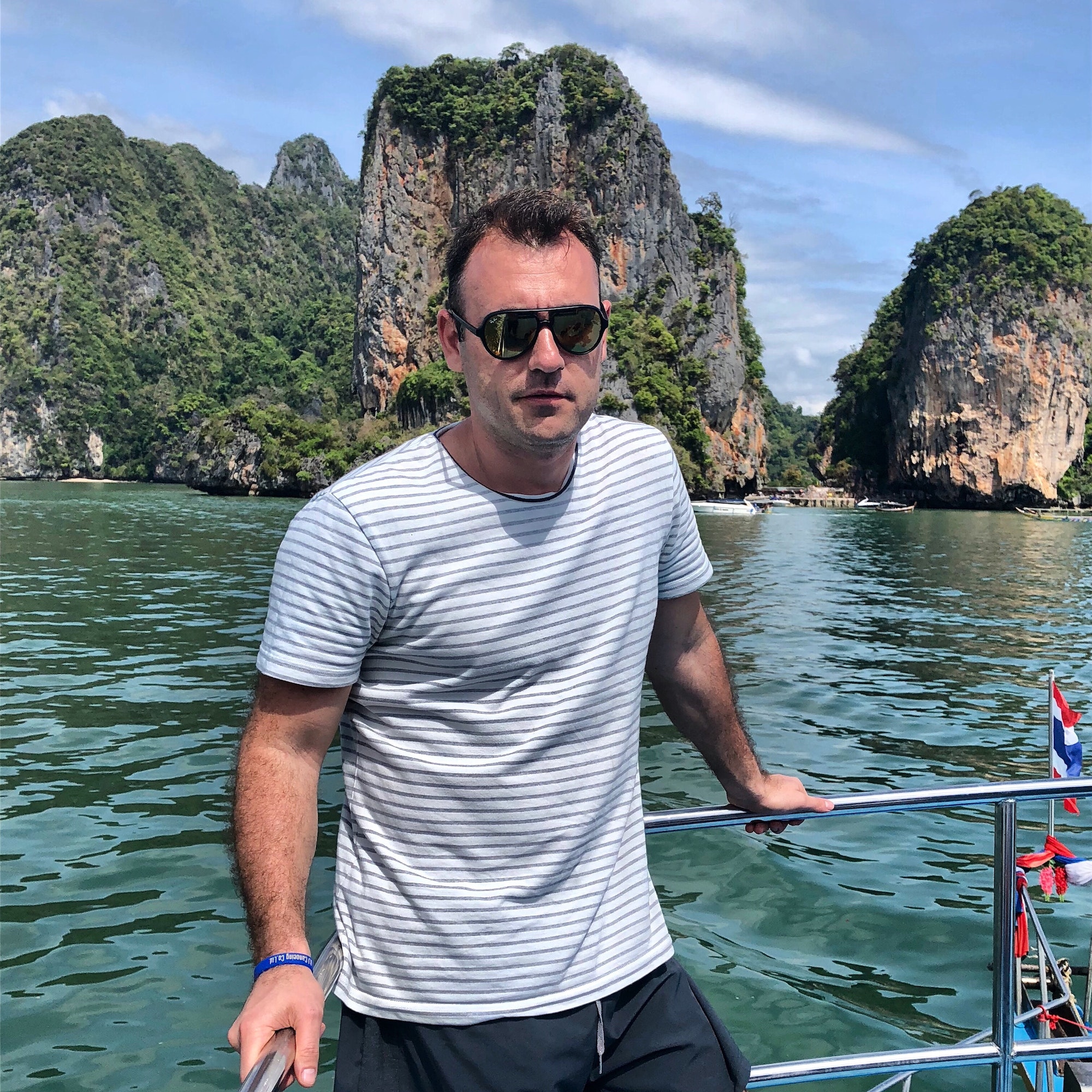
People Always Ask
What are Metal Spinning Parts and Their Applications
Metal spinning parts are components manufactured through the process of metal spinning, where a flat sheet of metal is rotated at high speeds while a tool or mandrel forms it into a desired shape. These parts are widely used in industries such as aerospace, automotive, plumbing, and consumer products due to their strength, precision, and cost-effectiveness. Applications range from fuel tanks and exhaust systems to decorative household items and industrial containers.
What are the Benefits of Using Metal Spinning in Manufacturing?
Metal spinning offers several benefits, including:
- Cost Efficiency: It can be more cost-effective than other forming processes for high-volume production.
- Material Savings: Minimal material waste due to the precision of the spinning process.
- Design Flexibility: Ability to create complex shapes and geometries that might be difficult or impossible with other methods.
- Strength and Durability: Spinning produces parts with high structural integrity and consistent wall thickness.
What Materials Can Be Used in Metal Spinning?
A variety of metals can be spun into parts, including:
- Stainless Steel: Known for its corrosion resistance and durability.
- Aluminum: Lightweight yet strong, suitable for aerospace and automotive applications.
- Brass and Copper: Often used for decorative and plumbing components due to their aesthetic appeal and corrosion resistance.
- Titanium: Ideal for high-performance applications requiring strength and lightweight properties.
What is the Difference Between Metal Spinning and Other Forming Processes?
Metal spinning differs from processes like stamping, forging, and casting in several ways:
- Spinning involves high-speed rotation and localized forming, which allows for greater precision and control over wall thickness.
- Stamping typically uses dies to press metal into shape, suitable for flat or relatively simple parts.
- Forging involves shaping metal through compressive forces, often used for high-strength applications.
- Casting involves pouring molten metal into molds, suitable for complex shapes but less precise than spinning.
How Does the Metal Spinning Process Work?
The metal spinning process involves several steps:
- Preparation: The metal sheet is cut to the appropriate size and shape.
- Chucking: The sheet is secured to a chuck, which rotates at high speeds.
- Forming: A tool or mandrel is applied to the rotating metal, gradually forming it into the desired shape.
- Finishing: The spun part may undergo additional processes such as trimming, grinding, or polishing to achieve the final specifications.
What Quality Control Measures are in Place During Metal Spinning?
Quality control in metal spinning includes:
- Inspection: Regular inspections during each stage of production to ensure dimensions, wall thickness, and surface finish meet specifications.
- Testing: Mechanical testing to verify the strength and durability of the spun parts.
- Certification: Compliance with industry standards and certifications, such as ISO, to ensure quality and reliability.
How Can I Optimize the Design for Metal Spinning?
To optimize a design for metal spinning:
- Consider Material Properties: Choose a material that is compatible with the spinning process and meets the performance requirements.
- Minimize Undercuts: Design parts with minimal undercuts to facilitate easy removal from the mandrel.
- Uniform Wall Thickness: Aim for consistent wall thickness to reduce material waste and improve part strength.
- Draft Angles: Include appropriate draft angles to allow for easy ejection from the tooling.
By incorporating these FAQs into your website, you can provide valuable information to potential customers and improve your SEO ranking on Google. Make sure to use relevant keywords throughout the content and consider linking to related pages or resources within your site for added SEO benefit.
Let's Work Together
We will contact you within 1 working day, please pay attention to the email with the suffix “@spinflange.com”